Engineering a Long-Term Solution for Warpage Control in Diamond Louvre Clips
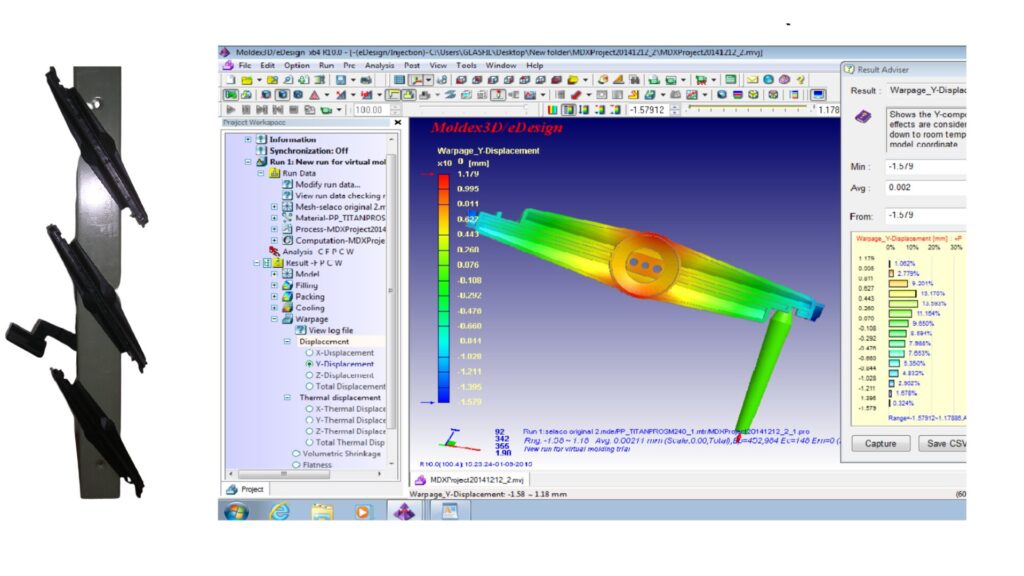
Client Background
A customer approached us to manufacture diamond louvre clips in three distinct colors: black, white, and grey. The clips were expected to maintain precise dimensions and consistent aesthetics across varying climates and long-term storage conditions.
The Challenge
While initial production met all dimensional specs with a tight warpage tolerance of ≤0.2mm, feedback from the field revealed dimensional changes occurring weeks after delivery. Over time, the clips experienced increased warpage after being stored in packaging, with measurements reaching up to 0.8mm in some cases.
Our Investigation
Committed to upholding the product’s long-term reliability, our engineering team conducted a full-scale diagnostic, including:
-
Controlled production trials under varied machine settings
-
Conditioning samples post-molding using different cooling and stabilization techniques
-
Simulation of post-delivery storage conditions
We also performed a commonality study across 62 samples to understand the material behavior. Using our Moldex (Moldflow simulation software) showed that standard PP grades would inherently exhibit warpage in the 0.4–0.5mm range. We altered the design of the louvre that would lower the warpage (X-Y direction warpage) The material specified by the customer, while offering aesthetic and rigidity advantages, contributed to additional internal stress buildup over time.
The Solution
Rather than defaulting to costly mold redesign, we explored material science innovations. Working closely with our material compounder, we developed a custom-engineered formulation designed to improve long-term dimensional stability:
-
Switched from PP Homo to PP Copolymer as the base resin
-
Incorporated 15% elastomer for better stress absorption without compromising strength
-
Added UV stabilizers and antioxidants to enhance color durability under prolonged exposure
The Result
-
-
Warpage stabilized to within accepted tolerance levels even after extended storage
-
Color integrity maintained over time, reducing returns and complaints
-
Customer resumed full-scale production confidently, with zero reported issues since implementation
-
If you have a problem with your plastic parts, feel free to contact us: info@glasfil.com or hit the WhatsApp Floating button to have a chat with our solution engineers.